Case Report: 22CA004
Contract Agricultural Worker Dies After Being Engulfed by Tons of Nuts
Download a PDF to print this report: Contract Agricultural Worker Dies After Being Engulfed by Tons of Nuts (PDF)ā
Summary
On September 8, 2022, a 47-year-old Hispanic male agricultural contract worker (the victim) was working in a tree nut processing facility labeling large (2200 pound) sacks of nuts near the end of the night shift. He went in search of shoe coverings, recalling that he had seen a box in an empty storage silo. When he did not return to his workstation, the site supervisor went looking for him and noticed about 50ā75 tons of nuts spilling out of the open access hatch to one of the 850 ton silos onsite.
The site supervisor called a team of co-workers to clean up the spill, and after a few minutes they found the unresponsive victim buried under the nuts. The site supervisor called 911 and several co-workers performed CPR until emergency services arrived. Paramedics arrived but were unable to revive the victim, and he died from asphyxiation.
Introāāduction
On September 8, 2022, at approximately 5 a.m., a 47-year-old Hispanic male agricultural contract worker died from asphyxiation after being buried under approximately 50ā75 tons of nuts that spilled out of the access hatch of an 850-ton storage silo. The CA/FACE investigator received notification of this incident on or around January 31, 2023, from the Cal/OSHA Weekly Fatality Report. On February 7, 2023, the CA/FACE investigator contacted the manager of the victimās employer (i.e., the local office of the staffing agency) who referred the agencyās investigator to her corporate headquarters. Multiple attempts to interview anyone at the staffing agency with knowledge of the incident were unsuccessful.
On March 14th, the CA/FACE investigator contacted the general manager of the nut processing facility (host employer). Shortly thereafter, the investigator was contacted by the law firm representing the host employer who informed the CA/FACE program that they (the law firm) would be the point of contact for the investigation. The CA/FACE investigator then requested the following information from the law firm, most of which was provided on May 15, 2023:
The host employerās Injury Illness Prevention Program (IIPP)
- New or contract employee site safety orientation training materials
- SOP or written program related to confined spaces
- SOP or written program for material storage and handling
- SOP or written program for personal protective equipment
- Training materials relating to the aforementioned
- Training records for the victim relating to the aforementioned written programs
- Incident reports, notes, photographs, or diagrams from the companyās internal investigation of this incidentā
On May 16, 2023, the CA/FACE investigators evaluated the incident scene and interviewed the host employer plant manager and site supervisor, who were both on scene at the time of the incident. The quality assurance/quality control manager, knowledgeable about site safety requirements), was also present at the time of the interview. The investigators were advised by the host employerās counsel that the other eyewitness (who were temporary workers) were no longer onsite and would not be available for an interview. The investigation also included an interview with the Cal/OSHA inspector, who conducted an onsite investigation the morning of the incident, and review of reports from both Cal/OSHA and the county coroner.
āEāmployer
This was a dual-employer workplace subject to Cal/OSHAās āDetermination of Citable Employerā requirements and Federal OSHAās āMultiemployer Citation Policy.ā
- The employer of the victim was a nationwide staffing agency that had approximately 18,000 employees. The company had been in business since 2017 and had about two dozen employees working onsite, divided over two 12-hour shifts, on the day of the incident.
- The host employer was a nut processing company who had ten permanent employees and used between 10ā24 contract workers depending on the season. They had been in business for three years at that location.
Written Safety Programs and Training
At the time of the incident, the victimās employer, the staffing agency, had an IIPP3 which is required for all businesses in California. The written IIPP addressed employee safety by identifying individual responsibility at the management, supervisory, and associate levels. It also addressed compliance, disciplinary procedures, conducting regular workplace inspections (to identify workplace hazards), health and safety training to employees prior to assignment (or as hazards are identified), correcting identified hazards, investigating accidents, and records maintenance.
The staffing agencyās IIPP also contained an internal requirement to conduct a JHA/safety assessment of new client sites to identify hazards and to āensure that the necessary safeguards are in place to perform the work safely.ā Although a brief client facility assessment was performed on April 8, 2022, by the staffing agencyās regional safety manager and did identify some safety issues related to the facility, the assessment did not identify any specific corrective actions, training or personal protective equipment related to the victimās work activities, nor did it identify the storage silos on site as permit-required confined spaces. Further, there was no record that indicated that the victim received any training from his employer (the staffing agency).
The host employer (nut processing company) also had an IIPP that adhered to Cal/OSHA requirements as well as both a hazard communication program (to address chemical hazards) and a heat illness prevention plan. They also maintained additional procedures that included the following:
- Code of safe work practices
- Persoāānal protective equipment
- Emergency situations
- Material handling
- Machine safeguard
- Electrical safety
- Ladder safety
- Chemical safety
- Tool safety
- Forklift operating procedures
- GMP requirements for food processing operations
The host employer also developed and implemented a silo procedure for working in and around silos, but this procedure was not in place at the time of the incident.
Training covered by these programs was provided through supervisor instruction and qualified co-worker trainers. Training records indicated that the victim received training in emergency procedures, general safety, and GMP from the host employer prior to the beginning of nut processing operations.
Worker Information
The victim was a 47-year-old Hispanic male contract agricultural contract worker who worked on the night shift performing various activities related to nut processing. He was hired on February 8, 2022, and had been working fulltime for approximately seven months. He had received training in emergency procedures, site safety requirements, and GMP requirements several months prior to the incident. The victimās primary language was Spanish, and the site training was also in Spanish.
Equipment
The primary piece of equipment involved in this incident was a GSIĀ® Brand storage bin (silo) that had a maximum capacity of 850 tons (Exhibits 1 through 4). The nuts, once delivered to the processing facility, were moved by a series of conveyor belts and screw conveyors (augers) through various pieces of equipment to clean, hull, dry, size and sort the nuts prior to storing them in the silos. The nuts were stored in the silos prior to packaging and shipment to customers. The fill capacity of the silos was monitored by computer controllers for the process equipment as well as view ports located on the sides of the silos.
Incident Scene
The incident scene was a well-lit outdoor storage area containing numerous silos and conveyor systems for transferring the nuts to and from the process equipment. Adjacent to the silo storage area was a process building where the nuts were segregated by size prior to being transferred into the silos, and a packaging line where the nuts were transferred from the silos into several different sized containers prior to shipment. There was no confined space warning sign on the silo doors prior to the incident.

Weather
The weather on the day and time of the incident was approximately 80 degrees Fahrenheit, with an average wind speed of about 5.0 mph [Weather Underground]. The weather is not believed to have been a contributing factor in this incident.ā
Investigation
The incident occurred near the end of the victimās shift. He began work at approximately 6 p.m. on the night shift and was due to end his shift around 6 a.m. According to witness statements, the victim was tasked with labeling āsuper sacksā which contained 2200 pounds of product, around 4:15 a.m. As these sacks were stacked on pallets, it was necessary for the victim to climb on top of the sacks to complete his tasks. Because the facility must adhere to GMP requirements for food processing operations, all workers were required to wear shoe coverings in the area. Although an adequate amount of shoe covers was provided in the storage closet near the victimās work area, the victim left the work area recalling that he had seen shoe covers in an empty silo that he was cleaning a few days prior.
At approximately 5 a.m., a co-worker noticed that the victim was missing and began looking for him. He notified the site supervisor, who dispatched another co-worker to also join the search. Around 5:20 a.m., one of the co-workers walked past the silo area and noticed that the access door to one of the 850-ton silos was open with a large quantity of nuts (approximately 50ā75 tons) spilling out. He then found the site supervisor and informed him of the spill. The supervisor called a team of co-workers to clean up the spillage, and after a couple of minutes, they found the victim unresponsive under the nuts. The site supervisor and several co-workers called 911 and performed CPR until emergency services arrived. Paramedics arrived but were unable to revive the worker and he was pronounced dead.
Cause of Death
The county coroner listed the cause of death as traumatic asphyxiation.
Contributing Factors
Occupational injuries and fatalities are often the result of one or more contributing factors or key events in a larger sequence of events that ultimately result in the injury or fatality. CA/FACE investigators identified the following issues as key contributing factors in this incident:
- The staffing agency did not conduct a thorough job hazard analysis to identify all hazards at their clientās facility.
- The staffing agency did not provide adequate safety training to the victim prior to his assignment.
- The staffing agencyās risk management program did not provide their client a copy of their āfacility safety assessmentā nor did they follow up with any safety recommendations.
- The host employer, at the time of the incident, lacked a procedure to manage silo entries (i.e., confined space), nor was the silo access door locked.
- The host employerās silo involved in this incident did not have an inward swinging inner door installed as a safety feature.ā
Recommendations/Discussion
CA/FACE investigators concluded that, to help prevent similar occurrences staffing agencies who provide temporary staffing, and operating nut processing facilities should:
Recommendation #1: Conduct a thorough JHA of their clientās operation, to include a site visit.
Discussion: In this incident, the victimās employer did conduct a client facility assessment prior to their employees beginning work onsite, but this assessment only identified the safety programs the client had in place. It did not achieve the objectives of a JHA, which are to identify all the hazards to which their employees might be exposed and recommend controls such as procedures, training, and personal protective equipment (PPE). Specifically, the employerās regional safety manager, who performed the assessment, failed to identify any hazards, especially the storage silos which meet the definition of permit-required confined spaces and are known to pose engulfment hazards. Although the agencyās employees needed to enter the silos to clean them, the regional safety manager failed to designate the silos as a confined space. If the employerās safety manager had identified the silos as permit-required confined space, with potential engulfment hazards, and provided the employees onsite training and instruction, this incident may have been prevented.
Recommendation #2: Ensure that all contract employees working at client sites are trained on both their companyās policies as well as the duties that they will perform at the client site, as part of the onboarding process.
Discussion: Under both California and Federal OSHA requirements, employers are obligated to provide adequate health and safety training to employees prior to their assignments8. In this incident, there was no evidence that the staffing agency provided any training to their employees, instead, they placed that responsibility on their client, the host employer. While the host employer is still required to provide health and safety training to all employees on site, it does not absolve the staffing agency from their requirements to provide training to their staff. If the contract employee had received training from his employer prior to assignment, this incident may have been prevented.
Recommendation #3: Following any client site assessments or JHA, staffing agencies should share their findings with their clients and develop an action plan to address identified hazards, training, and personal protective equipment.
Discussion: While the staffing agency did conduct a client facility assessment, they did not share their findings with their client. We recommend that staffing agencies employ or engage the services of a competent health and safety professional to identify all the hazards to which their employees might be exposed and recommend procedures, training, and personal protective equipment to ensure that contract workers are not unnecessarily exposed to workplace hazards. Providing a workplace health and safety action plan to their clients not only protects their contact staff but benefits their clients as well. If the staffing agency had conducted a thorough JHA and formulated an action plan to address hazards training and PPE, this incident may have been prevented.
CA/FACE investigators also concluded that, to help prevent similar occurrences, employers in agricultural nut processing facilities should:
Recommendation #4: Ensure that storage silos are fitted with inward swinging inner access doors.
Discussion: In this case, the victim had opened the outer access door to a silo that was filled near capacity. Inward swinging doors (Exhibit 5) are a safety feature that ensures if the silo is filled with product, the pressure on the doors from the weight of the product prevents the doors from opening. If the silo had been fitted with inward swinging access doors, this incident may have been prevented.
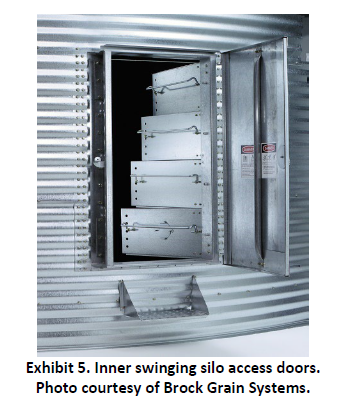
Recommendation #5: Develop and implement a procedure to manage and control unauthorized silo entries.
Discussion: In this incident, the victim attempted to enter a silo by himself not knowing that it contained an engulfment hazard. All silos are considered confined spaces and most, depending on the contents and potential for a hazardous atmosphere, are considered permit-required confined spaces.
A permit-required confined space is defined as a confined space that has one or more of the following characteristics:
- Contains or has a potential to contain a hazardous atmosphere
- Contains a material that has the potential for engulfing an entrant
- Has an internal configuration such that an entrant could be trapped or asphyxiated by inwardly converging walls or by a floor which slopes downward and tapers to a smaller cross-section, or
- Contains any other recognized serious safety or health hazard
Even if a silo is empty, it still may contain a hazardous or oxygen deficient atmosphere. Silos, like all confined spaces may be declassified if the only hazard is atmospheric and can be controlled by ventilation.
Specific to this incident, employers of nut processing facilities should, at minimum, have a silo entry procedure that includes the following:
- Posting warning signs on all silo entrance hatched to read āDanger! Potential atmospheric and engulfment hazards. Do not enter without management authorizationā or similar language.
- Keep all silo doors locked except when entering, and only provide keys to trained, authorized individuals.
- Only allow workers trained in the silo procedure to enter. The training should detail circumstances where entry is permissible and when it is not.
- Conduct atmospheric testing prior to entry. If the silos have built-in fans, test each silo at least once to ensure that the fans are providing adequate ventilation to maintain a safe atmosphere.
- Entries, even for declassified confined spaces, should never be done alone. As with any hazardous operation, one of more additional workers should be on scene to provide aid should conditions change.ā
If the employer had signage, a procedure and restricted access to the silo at the time of the incident, this incident may have been prevented.
DisclaimerMention of any company or product does not constitute endorsement by California FACE and the National Institute for Occupational Safety and Health (NIOSH). In addition, citations to websites external to California FACE and NIOSH do not constitute NIOSH endorsement of the sponsoring organizations or their programs or products. Furthermore, California FACE and NIOSH are not responsible for the content of these websites. All web addresses referenced in this document were accessible as of the publication date.
References
Investigator Information
This investigation was conducted and authored by Robert Kleinerman, MPH, CIH, Fatality Investigator/Consultant; and Jacqueline Chan, MPH, CDPH Industrial Hygienist. Additional contributions to the report were provided by Robert Harrison, MD, MPH, CDPH FACE Project Officer; Laura Styles, MPH, FACE Research Scientist; and Glenn Shor, PhD, Cal/OSHA CFOI Program.ā