Case
Report: 19CA003
A water truck operator died after being struck by a pressurized hose
Download a PDF to print this report: A water truck operator died after being struck by a pressurized hose (PDF)
Summary
A water truck operator (the victim) died after being struck by a pressurized water hose. The victim was filling up a water truck with water from a hydrant that was connected to a water tank when the incident occurred. The hose that was used to make the transfer was not of sufficient strength or type to accommodate the water pressure involved. The normal procedure was to first open the valve on the truck followed by the valve on the hydrant. On the day of the incident, the valve on the truck was not opened. The CA/FACE investigator determined that, in order to prevent similar incidents, employers with workers who operate water trucks should:
Ensure that the machinery and equipment provided to transfer high-pressure water can safely withstand all reasonably anticipated loads.
Implement policies and procedures as part of a safety program to ensure that unsafe conditions are identified, and safe work practices are followed.
Introduction
On August 19, 2019, at approximately 3:00 p.m., a 67-year-old male water truck operator, working as a seasonal employee, sustained severe head injuries when a pressurized water hose burst and he was knocked to the ground. He died two days later from his injury. The CA/FACE investigator received notification of this incident on August 29, 2019 from the Cal/OSHA Weekly Fatality Report. On August 30, 2019, contact was made with the employer of the victim. On September 5, 2019, the CA/FACE investigator traveled to the location where the incident occurred and interviewed the general manager, the victimās supervisor, and the safety supervisor. The county coroner, fire department, and sheriffās department report of the incident were also obtained and reviewed.
Employer
The employer of the victim was a cooperative of almond growers that provided hulling and shelling services to grower members. The cooperative had 550 almond grower members and had been in business since 1966. The cooperative had 95 employees; 18 were full time and the remainder were seasonal workers.
Written Safety Programs and Training
The cooperative had a written injury and illness prevention program (IIPP) with all the essential elements required by law. Safety meetings were held on a monthly basis and were documented. The safety supervisor provided all safety and other trainings for staff. The victim had received training on the proper procedures for transferring water and had done this task many times in the past. The seasonal workers began working during the first week of August and already attended the cooperativeās mandated safety meeting.
Worker Information
The victim was a 67-year-old water truck operator for the cooperative. He had worked 40 hours per week on a seasonal basis for the past six years.
Description of Work
The victim was performing dust control by spraying water on the almond fields that surrounded the facility using the cooperativeās water truck. When the water in the truck was empty, he would normally refill it at the designated hydrant. However, because the groundwater supply was low, the normal hydrant used was not available. Arrangements were made with a neighboring business to use their water system which included a 500,000-gallon water storage tank which supplied water at a higher pressure. The normal procedure was to connect the hose (provided with the water truck) to the water tank hydrant outlet ball valve, then to the inlet ball valve on the truck. Once the hose was secured in place, the ball valve on the truck was to be opened first, followed by the ball valve on the hydrant. Water would then flow from the tank to the truck under a pressure that varied from 125 -140 psi.
Investigation
On the day of the incident, the victim was filling the water truck from the hydrant of the neighborās water tank (Exhibit 1). The victim used a thermoplastic rubber bulk water discharge hose with polyethylene helix reinforcement that was provided with the water truck (Exhibit 2). This hose was only designed to withstand a maximum working pressure of 50 psi, which was in the range of the normal groundwater supply. He connected the hose to the truck and hydrant, then opened the hydrantās outlet ball valve. Unlike the normal procedure, the victim did not open the inlet ball valve on the truck (Exhibit 3). As he was attempting to fill the truck, the hose burst and struck the victim, causing him to fall to the ground and strike his head. The safety supervisor was walking by the water truck and noticed the victim on the ground. The supervisor shut the hydrant off and notified another manager who then called 911. The supervisor performed CPR on the victim until the paramedics arrived and transported him to a local hospital. He died from his injuries two days later.
Cause of Death
According to the medical records, the cause of death was skull fracture with intracranial bleed.
Recommendations
The CA/FACE investigator determined that, in order to prevent similar incidents, employers with workers who operate water trucks should:
Recommendation #1: Ensure that the machinery and equipment provided to transfer high-pressure water can safely withstand all reasonably anticipated loads.
Discussion: In this incident, the hose used to transfer water from the water tank to the truck was a thermoplastic rubber bulk water discharge hose with polyethylene helix reinforcement (Exhibit 4). This type of hose can only withstand a maximum working pressure of 50 psi. A more adequate hose would have been an ethylene propylene diene monomer (EPDM) bulk water discharge hose with spiral-plied synthetic fabric reinforcement, a vinyl nitrile water discharge hose with wire helix reinforcement, or a polyvinyl choloride (PVC) bulk water hose with a rigid PVC helix reinforcement. EPDM bulk water discharge hoses are used for pumping water in quarries, mines, construction sites, and other abrasive environments and can withstand working pressures up to 300 psi. This type of hose was not on the truck and thus not available for the victim to use. Had a hose with the proper design been used to fill the truck, pressure from the hydrant would not have caused the hose to burst, thereby preventing this incident.
Recommendation #2: Implement policies and procedures as part of a safety program to ensure that unsafe conditions are identified, and safe work practices are followed.
Discussion: In this incident, the victim began transferring water from the hydrant without first opening the intake ball valve on the truck. Because this valve was not turned on first, pressure in the hose caused it to swell and then burst, knocking the victim to the ground.
The victim was an experienced seasonal employee and had transferred water safely on numerous occasions in the past. However, this type of water transfer was not the typical source that was used. The employer had written safety procedures and training that included the safe transfer of water. Their correct procedure was to first connect the hose to the water tank hydrant outlet ball valve, then to the inlet ball valve on the truck. Once the hose was secured in place, the ball valve on the truck was to be opened first, followed by the ball valve on the hydrant. In this incident, the victim connected the hose to the truck and hydrant, then he opened the water tank valve but did not open the valve on the truck. Although the employee had received safety training, there was no communication or method to ensure that the proper procedure occurred. For example, written check-off sheets and/or periodic and regular safety audits with direct observation can be used to ensure that safe work practices are followed. In addition, employee safety training should be verified through written testing, oral confirmation, or demonstration. If these procedures had been implemented, the victim may have realized that the truck valve was not open, and this incident could have been prevented.
Exhibits
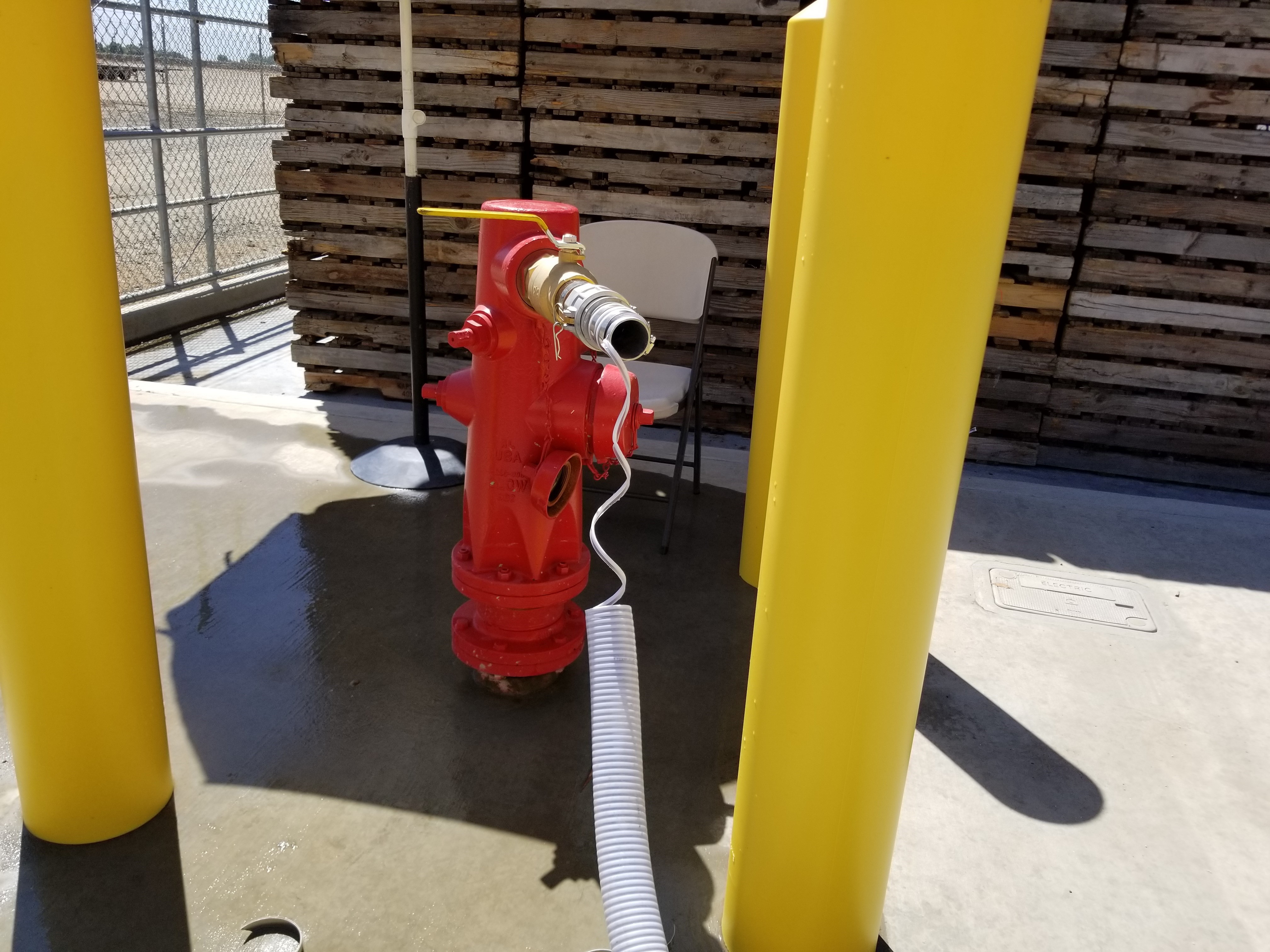
Exhibit 1. The fire hydrant involved in the incident.
Exhibit 2. The hose connected to the water truck.
Exhibit 3. The inlet ball valve on the rear of the water truck.
Exhibit 4. A portion of the hose involved in the incident.
References
California Code of Regulations, Title 8, Subchapter 7. General Industry Safety Orders, Group 1.
General Physical Conditions and Structures Orders, Introduction.
§3203. Injury and Illness Prevention Program
Group 2. Safe Practices and Personal Protection
Article 7. Miscellaneous Safe Practices
§3328. Machinery and Equipment
Authors
Hank Cierpich, FACE Investigator
Robert Harrison, MD, MPH, FACE Project Officer
Laura Styles, MPH, Research Scientist
June 19, 2020